Robotics is a field that has seen exponential growth in recent years, with robots being used in various industries such as manufacturing, healthcare, and even space exploration. These machines are designed to automate tasks, increase efficiency, and improve precision. However, behind the seemingly flawless movements of these robots lies a complex system known as robot kinematics.
Robot kinematics is a branch of robotics that deals with the study of motion and position of robots. It involves understanding the principles of mechanics and applying them to the design and control of robotic systems. In this blog post, we will dive into the world of robot kinematics, exploring its types, applications, and future developments.
Overview of Robot Kinematics
Robot kinematics is based on the principles of classical mechanics, which explains the relationship between forces and motion. In simple terms, it studies how robots move and perform tasks based on their design and control mechanisms. This involves analyzing the movement of individual parts of a robot, also known as its links, and determining the overall motion of the robot.
The study of robot kinematics can be divided into two main categories: forward kinematics and inverse kinematics. Forward kinematics deals with determining the position and orientation of a robot’s hand or end effector based on the angles and lengths of its joints. On the other hand, inverse kinematics involves calculating the joint angles required to achieve a desired position and orientation of the end effector.
Robot kinematics also takes into account external factors such as the environment and obstacles, which may affect the movement of the robot. This requires the use of sensors and advanced algorithms to enable robots to adapt and make decisions based on their surroundings.
Types of Robot Kinematics
There are several types of robot kinematics, each with its own specific features and applications. Let’s take a closer look at some of these types below:
Cartesian or Rectilinear Kinematics
Cartesian or rectilinear kinematics is based on the Cartesian coordinate system, which uses three axes (x, y, and z) to describe the position of a point in space. In this type of kinematics, the end effector’s position is defined by its coordinates relative to the robot’s base. This allows for precise control over the robot’s movements, making it suitable for applications that require high accuracy.
Cylindrical Kinematics
Cylindrical kinematics, also known as polar kinematics, uses a cylindrical coordinate system to define the position of the end effector. It involves the rotation of a joint along a fixed axis and translation along another axis. This type of kinematics is commonly used in machines that require circular motion, such as robotic arms in assembly lines.
Spherical Kinematics
Spherical kinematics is similar to cylindrical kinematics in that it uses a spherical coordinate system to define the position of the end effector. However, instead of two axes, it uses three axes (theta, phi, and r) to determine the orientation of the end effector. This type of kinematics is commonly used in robotics applications that require a high degree of flexibility, such as space exploration.
SCARA Kinematics
SCARA (Selective Compliance Assembly Robot Arm) kinematics is a type of parallel kinematics that uses a combination of rotary and linear joints to achieve both vertical and horizontal movements. This type of kinematics is commonly used in pick and place tasks in manufacturing processes.
Delta Kinematics
Delta kinematics, also known as inverse parallel mechanics, is a type of parallel kinematics that uses multiple interconnected arms to achieve precise movement. This type of kinematics is commonly used in 3D printing and packaging applications.
Forward Kinematics
Forward kinematics is the process of determining the position and orientation of a robot’s end effector based on the angles and lengths of its joints. This involves using the Denavit-Hartenberg (DH) convention, which provides a mathematical framework for representing robot kinematics.
The DH convention assigns a coordinate frame to each joint of the robot, with a set of parameters defining the transformation between adjacent frames. These parameters include the link length, twist angle, offset distance, and joint angle. By using these parameters, the forward kinematics equations can be derived to determine the position and orientation of the end effector.
Forward kinematics is essential for controlling the movement of robots in tasks such as welding, painting, and assembly. It allows engineers to program the desired positions of the robot’s end effector, enabling it to perform precise movements in a controlled manner.
Inverse Kinematics
Inverse kinematics is the process of calculating the joint angles required to achieve a desired position and orientation of the end effector. Unlike forward kinematics, which determines the end effector’s position based on joint angles, inverse kinematics uses the end effector’s position to calculate the joint angles.
Inverse kinematics is crucial for tasks that require the robot to adapt to different positions and orientations, such as manipulating objects or performing tasks in a cluttered environment. It enables robots to make decisions based on their surroundings and adjust their movements accordingly.
To solve the inverse kinematics problem, several approaches can be used, including analytical solutions, numerical methods, and heuristic algorithms. The choice of method depends on the complexity of the robot’s design and the task at hand.
Applications of Robot Kinematics
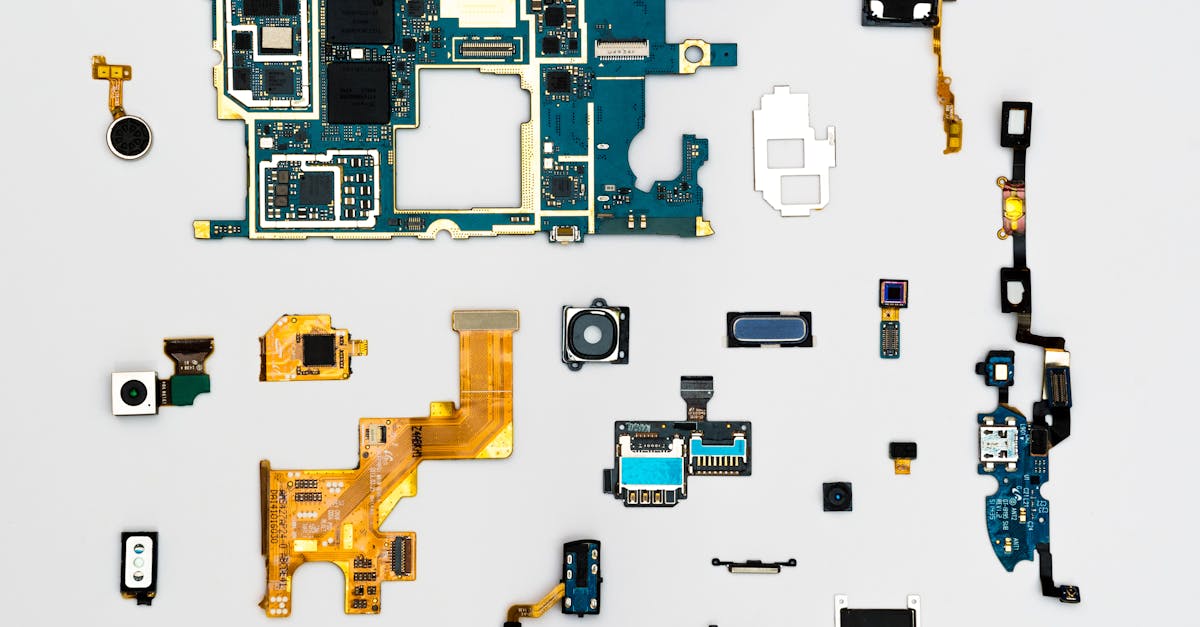
Robot kinematics has numerous applications in various industries, including manufacturing, healthcare, and space exploration. Let’s take a look at some of these applications below:
Manufacturing
Robots have become an indispensable part of many manufacturing processes due to their speed, precision, and repeatability. In this industry, robot kinematics is used to design and control robots for tasks such as welding, painting, and assembly. By using robot kinematics, manufacturers can improve production efficiency and reduce human errors.
Healthcare
Robotics has also made significant advancements in the healthcare industry, with robots being used for surgeries, rehabilitation, and drug delivery. Robot kinematics plays a crucial role in these applications, as precise movements are needed to ensure the safety of patients. For example, in surgery, robots can be programmed to perform minimally invasive procedures, reducing the risk of complications and speeding up recovery time.
Space Exploration
Robot kinematics has enabled humans to explore the depths of space, with robots being used in missions to other planets and moons. These machines are equipped with advanced sensors and algorithms that enable them to adapt to different terrains and make decisions based on their surroundings. Robot kinematics plays a vital role in the design and control of these robots, enabling them to carry out tasks such as collecting data, analyzing samples, and even building structures.
Challenges and Future Developments
Despite its numerous applications and advancements, robot kinematics still faces several challenges, especially in highly complex tasks and environments. One of the main challenges is achieving real-time control of multiple degrees of freedom (DOF) in a robot. This requires high computational power and advanced control algorithms to ensure smooth and accurate movements.
Another challenge is the integration of external factors, such as obstacles and changing environments, into the robot’s movements. This requires the use of advanced sensors, machine learning, and artificial intelligence to enable robots to adapt and make decisions in real-time.
In the future, we can expect to see further developments in the field of robot kinematics, with advancements in control techniques and sensor technologies. This will lead to more efficient and versatile robots that can handle complex tasks and operate in dynamic environments.
Conclusion

Robot kinematics is a fascinating field that plays a crucial role in the design and control of robots. It involves understanding the principles of mechanics and applying them to enable robots to move and perform tasks accurately. With its numerous applications in various industries, robot kinematics has revolutionized the way we live and work.
In this blog post, we have explored the different types of robot kinematics, including Cartesian, cylindrical, spherical, SCARA, and delta kinematics. We have also discussed the importance of forward and inverse kinematics and their applications in tasks such as manufacturing, healthcare, and space exploration. Finally, we looked at some of the challenges faced by robot kinematics and the future developments that we can expect in this field.
Robot kinematics will continue to evolve and advance, paving the way for more sophisticated and intelligent robots in the future. As technology continues to progress, we can only imagine the endless possibilities that lie ahead for the field of robot kinematics.