Automated production lines have become an integral part of modern manufacturing, driving innovation and shaping the landscape of industries. The concept of automation in industry can be traced back to the early days of the Industrial Revolution, when the emergence of power-driven machinery paved the way for assembly lines. However, it was not until the mid-20th century that we saw the true revolution in automated production lines with the introduction of programmable logic controllers (PLCs) and industrial robots. These advanced technological systems have transformed the manufacturing process, offering increased efficiency, productivity, and flexibility.
In this ultimate guide to industrial robotics and automation, we will delve deep into the world of automated production lines and explore their evolution, components, types, applications, benefits, challenges, and future trends. We will also look at case studies of successful integration of industrial robotics and discuss best practices for implementing them. So, join us on this journey as we unravel the power and promise of automated production lines.
Evolution of Automation in Industry
The concept of automation in industry can be traced back to the 18th and 19th centuries, where steam-powered machinery and waterwheels were used in factories to perform repetitive tasks. However, it was not until the early 20th century that we saw the first assembly line being implemented by Henry Ford for his Model T car production. This marked the beginning of mass production through mechanization.
The next major milestone in the evolution of automation was the introduction of programmable logic controllers (PLCs) in the 1960s. These electronic devices allowed for the automation of processes through computer programming, making it easier for manufacturers to control and monitor their production lines.
The late 1960s and early 1970s saw the emergence of the first industrial robots, which were used for tasks such as welding, painting, and material handling. These robots were mainly hydraulic and pneumatic and lacked the precision and versatility of modern-day industrial robots.
With the advancements in technology and the need for more efficient and flexible production processes, the 1980s saw the emergence of the first computer-controlled industrial robots. These robots were able to perform complex tasks with accuracy, speed, and repeatability, making them ideal for industries such as automotive, electronics, and pharmaceuticals.
Fast forward to today, and we see a wide range of advanced industrial robots that can be programmed to perform a variety of tasks with minimal human intervention. The evolution of automation in industry has been driven by the constant need for increased efficiency, productivity, and flexibility, and it is showing no signs of slowing down.
Key Components of Industrial Robots
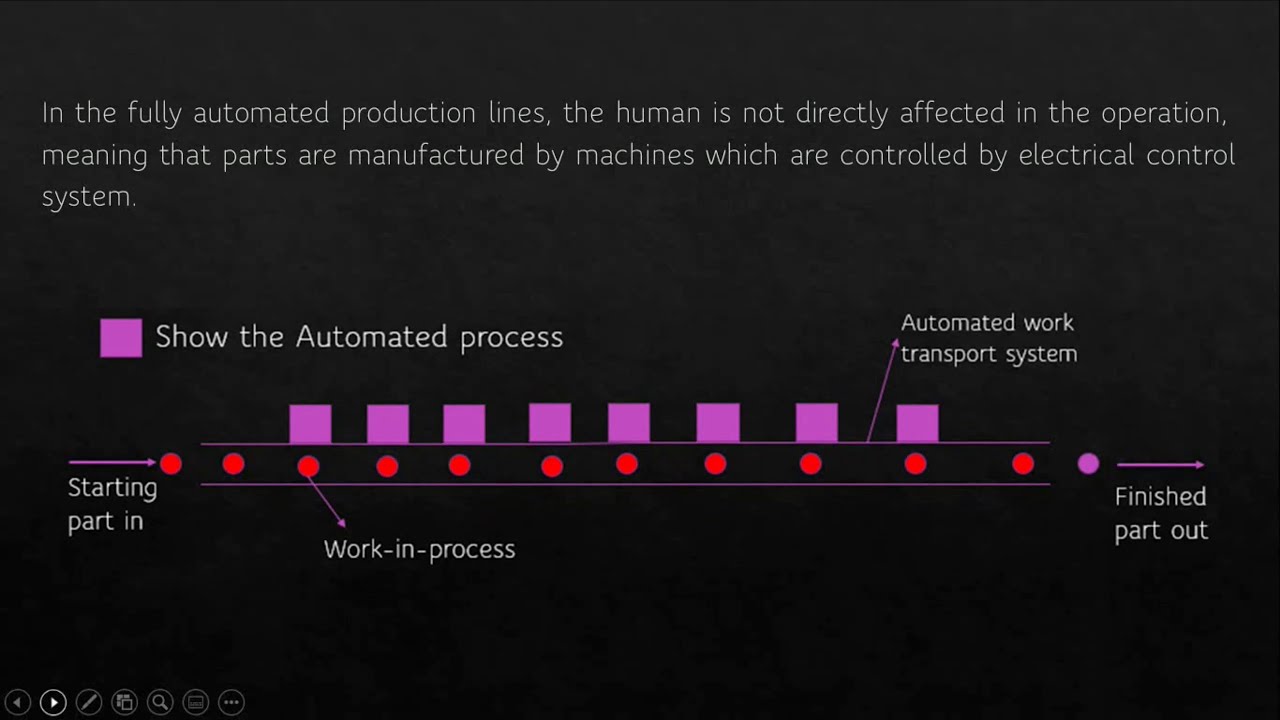
Industrial robots are complex machines made up of various components that work together to carry out specific tasks. Understanding these components is crucial in designing and implementing an efficient automated production line. The key components of industrial robots include:
Controller
The controller is the brain of the robot, responsible for interpreting the programmed instructions and controlling the movement and actions of the robot. It also monitors feedback from sensors and makes adjustments accordingly.
End Effector
Also known as the robot’s “hand,” the end effector is the part of the robot that interacts with the objects or materials being handled. This could be grippers, suction cups, or cutting tools, depending on the task at hand.
Sensors
Sensors play a crucial role in the functionality of industrial robots. They provide real-time feedback to the controller, allowing the robot to make precise movements and adjustments. Some common types of sensors used in industrial robotics include proximity sensors, vision sensors, and force/torque sensors.
Actuators
Actuators are responsible for converting electrical signals from the controller into mechanical motion. This allows the robot to move its joints and perform its designated tasks.
Power Supply
Industrial robots require a steady and reliable power supply to operate efficiently. The power supply also needs to be able to handle the electrical demands of the robot.
Types of Industrial Robots
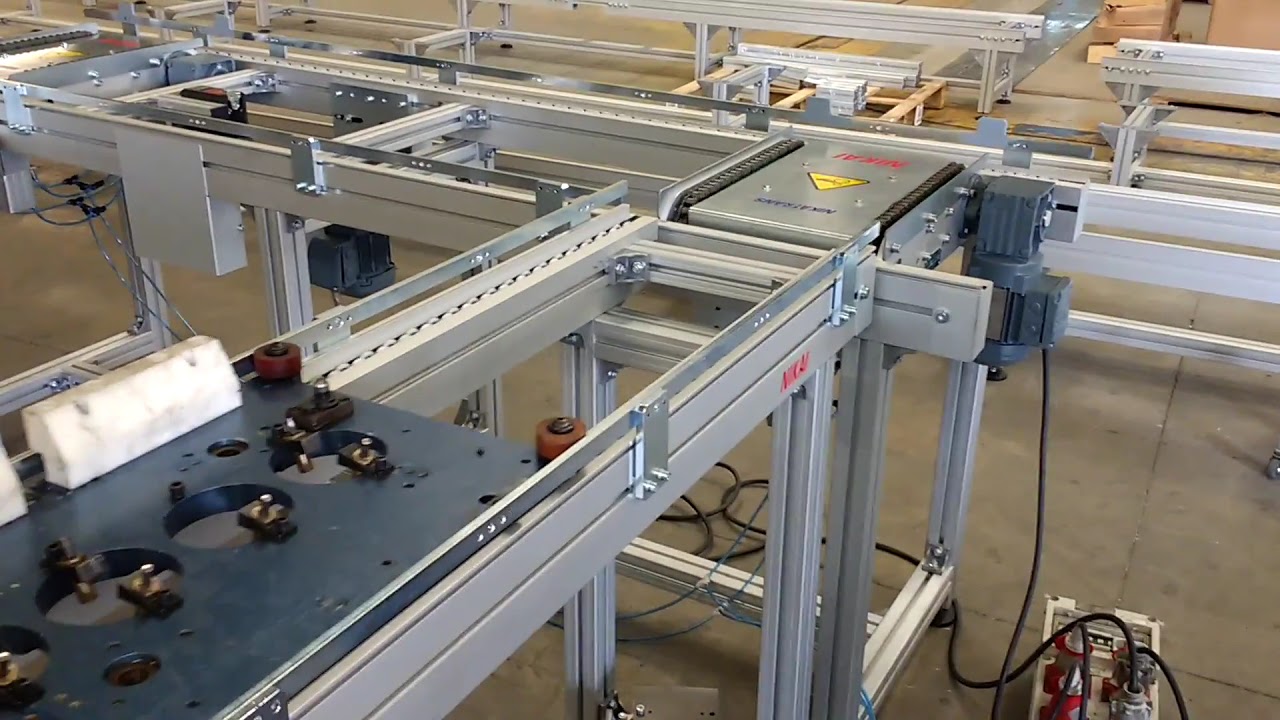
Industrial robots can be classified into several types based on their structure, movement, and application. Some common types of industrial robots include:
Cartesian Robots
Also known as gantry robots, cartesian robots have three linear joints that move along three axes – X, Y, and Z. They are best suited for pick-and-place applications.
SCARA Robots
SCARA (Selective Compliance Assembly Robot Arm) robots have two parallel rotary joints and one linear joint, giving them a “S”-shaped arm. They are best suited for assembly and packaging tasks.
Articulated Robots
Articulated robots have multiple rotary joints, allowing for a wide range of motion and flexibility. They are often used in welding, painting, and material handling applications.
Delta Robots
Delta robots have a unique design with three arms connected to a base, forming a delta shape. They are best suited for high-speed pick-and-place applications.
Collaborative Robots
Collaborative robots, also known as cobots, are designed to work alongside humans in a shared workspace. They have built-in safety features that allow for safe human-robot interaction.
Applications of Industrial Robotics
The use of industrial robots is not limited to a specific industry or application. These versatile machines can be found in various sectors, from automotive and electronics to healthcare and food processing. Some common applications of industrial robotics include:
Material Handling
One of the most common applications of industrial robots is material handling. They can handle materials of different shapes, sizes, and weights with precision and speed, making them ideal for tasks such as palletizing, packaging, and sorting.
Welding
Industrial robots are widely used in welding applications, where they offer increased precision, speed, and repeatability compared to manual welding. They are commonly used in the automotive, aerospace, and shipbuilding industries.
Painting and Coating
Painting and coating applications require high levels of precision and consistency, making industrial robots a perfect fit. They can apply paint or coatings evenly and with minimal overspray, resulting in a high-quality finish.
Assembly
With the ability to perform repetitive tasks with precision, industrial robots are well-suited for assembly operations. They can handle delicate components and have the flexibility to adapt to different assembly processes.
Inspection and Quality Control
The use of vision sensors in industrial robots allows for automated inspection and quality control. Robots can be programmed to detect defects or anomalies and make necessary adjustments, resulting in improved product quality and reduced waste.
Benefits of Industrial Automation
The integration of industrial robotics and automation offers a wide range of benefits for manufacturers, including increased efficiency, productivity, and flexibility.
Increased Efficiency
Industrial robots can work at high speeds without breaks, fatigue, or errors, resulting in increased efficiency and output. They can also handle dangerous, repetitive, or complex tasks, freeing up human workers to focus on more critical responsibilities.
Improved Productivity
By automating repetitive and time-consuming tasks, industrial robots can significantly increase productivity. This results in higher output levels and faster production cycles, allowing manufacturers to meet increasing demand while reducing lead times.
Flexibility
One of the main advantages of industrial robots is their versatility. They can be reprogrammed to perform different tasks, making it easy for manufacturers to adapt to changing production needs without significant downtime.
Higher Quality Products
Industrial robots offer precise and consistent movements, resulting in improved product quality and fewer defects. They can also perform detailed inspections and make necessary adjustments, further enhancing product quality.
Cost Savings
While the initial investment in industrial robots and automation may seem high, the long-term cost savings are significant. With increased efficiency, productivity, and quality, manufacturers can reduce costs associated with labor, waste, and downtime.
Challenges in Implementing Robotics and Automation
Despite the numerous benefits of industrial robotics, there are also challenges that manufacturers may face when implementing them. Some common challenges include:
High Initial Investment
The cost of industrial robots and automation can be a significant barrier for small to medium-sized businesses. The initial investment can run into hundreds of thousands of dollars, making it difficult for some companies to adopt this technology.
Integration with Existing Systems
Integrating industrial robots and automation into existing production lines can be a complex process. It requires careful planning and coordination to ensure compatibility and minimal disruption to production processes.
Need for Skilled Personnel
While industrial robots can perform tasks autonomously, they still require skilled personnel to program, maintain, and troubleshoot. This can be a challenge for manufacturers who may not have the necessary expertise in-house.
Safety Concerns
As industrial robots become more advanced and work alongside humans, safety becomes a crucial consideration. Manufacturers need to ensure proper safety protocols and measures are in place to protect both human workers and robots.
Future Trends in Industrial Robotics
The future of industrial robotics and automation looks promising, with advancements in technology and increasing demand for efficient and flexible production processes driving innovation. Some key trends we can expect to see in the coming years include:
Collaborative Robotics
Collaborative robots are gaining popularity, especially in industries where humans and robots need to work together. With built-in safety features and improved sensing capabilities, these robots offer new possibilities for human-robot collaboration.
Mobile Robotics
Mobile robots, also known as autonomous mobile robots (AMRs), are becoming more prevalent in manufacturing facilities. These robots can navigate independently and carry out tasks such as material transportation, freeing up human workers for more critical responsibilities.
Artificial Intelligence (AI) and Machine Learning
The integration of AI and machine learning in industrial robots is set to revolutionize the manufacturing process. These technologies will allow robots to learn from their surroundings, make decisions, and adapt to changing conditions.
3D Printing
While not a new technology, the use of 3D printing in industrial robotics is gaining traction. The ability to print custom end effectors and components on-demand can significantly improve the flexibility and efficiency of industrial robots.
Case Studies of Successful Automation
Over the years, we have seen numerous examples of successful integration of industrial robotics and automation in different industries. Let’s take a look at some notable case studies:
Tesla
Tesla has fully embraced industrial robotics and automation in its production of electric vehicles. The company uses over 160 robots in its Model S production line, decreasing the assembly time for each vehicle from around 3 days to just 3 hours.
Amazon
Amazon has been using robots in its warehouses since 2012 to assist with order fulfillment. These robots can move shelves of inventory around the warehouse, allowing for faster and more efficient picking and packing processes.
Boeing
Boeing has incorporated industrial robots in the production of its aircraft, including its flagship 777X model. The robots are used for tasks such as drilling, riveting, and handling large parts, resulting in increased efficiency and quality.
Best Practices for Integrating Industrial Robotics
The successful integration of industrial robots and automation requires careful planning and implementation. Some best practices to consider include:
- Clearly define the goals and objectives of automation and robotics in your production process.
- Conduct a thorough analysis of existing processes and identify areas where robots can add the most value.
- Choose the right type of robot for the task at hand.
- Develop a detailed plan for integrating robots into existing systems and workflows.
- Train personnel to program, operate, and maintain the robots effectively.
- Implement proper safety measures and protocols.
- Continuously monitor and optimize the performance of the robots.
Conclusion
Automated production lines have come a long way since the early days of assembly lines, and industrial robotics is at the forefront of this revolution. With the ability to improve efficiency, productivity, flexibility, and product quality, industrial robots are reshaping the manufacturing landscape. While there may be challenges in implementing this technology, the potential benefits far outweigh them. As we look to the future, we can expect to see even more advancements in industrial robotics, driving innovation and transforming industries. So, embrace automation and take your production processes to the next level.