The dawn of the 21st century has witnessed a surge in technological advancements, with artificial intelligence, automation, and robotics taking center stage. Among these, industrial robotics stands out as a key driver of economic growth, productivity gains, and a paradigm shift in the manufacturing landscape. This article delves into the multifaceted world of industrial robotics, exploring its history, current applications, economic impact, and the future it promises.
Introduction to Industrial Robotics
Industrial robots, also known as manufacturing robots, are programmable machines that are designed to automate various tasks within a production process. They are used to perform repetitive, dangerous, and precise tasks with high efficiency and accuracy. These robots are equipped with specialized end-effectors, sensors, and controllers, allowing them to carry out a wide range of tasks such as welding, painting, material handling, assembly, and inspection. Industrial robotics has revolutionized the manufacturing industry by increasing productivity, reducing costs, and improving product quality.
History of Industrial Robotics
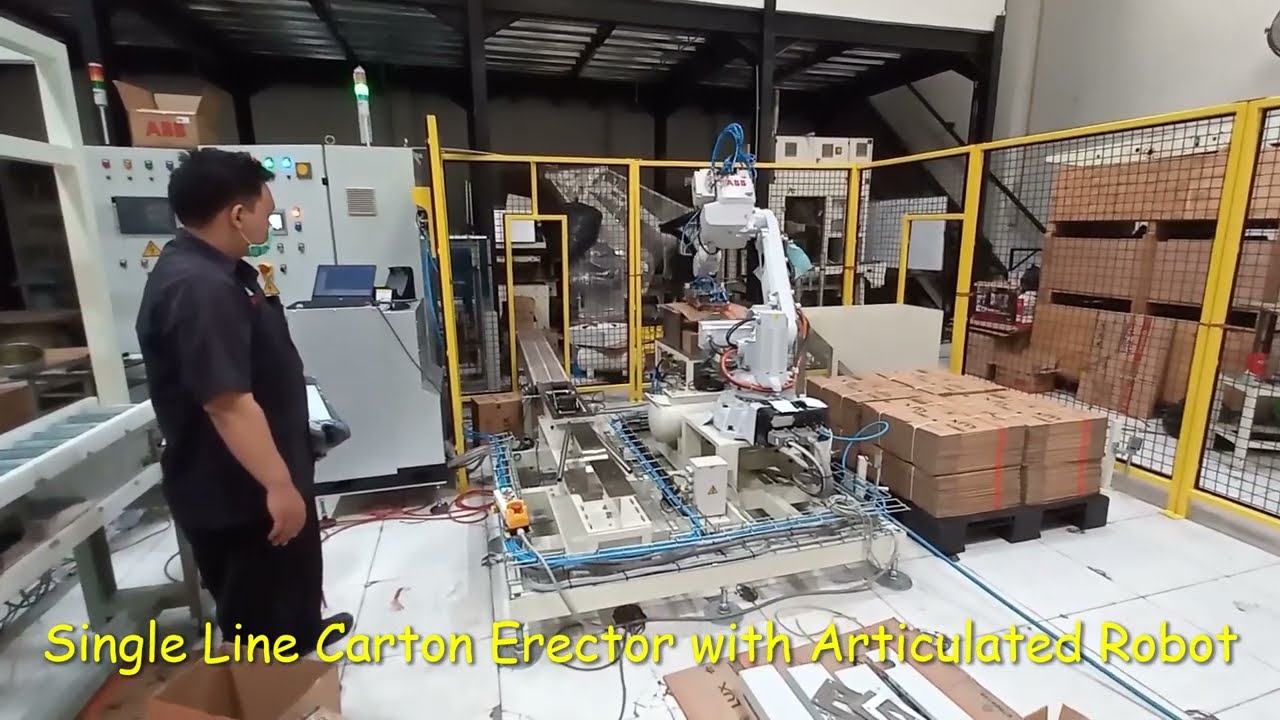
The concept of automated machines can be traced back to ancient Greek mythology, where the legend of Talos, a giant automaton, first sparked the human imagination. However, the practical realization of industrial robotics began in the mid-20th century. The 1950s saw the development of the first programmable robots, capable of performing simple tasks like welding. These early robots were bulky, slow, and limited in their capabilities, but they marked the beginning of a new era.
In the 1960s, General Motors (GM) became the first company to successfully implement industrial robots on a large scale. GM introduced a robot named Unimate, which was used for spot welding in their production line. This marked the widespread adoption of industrial robots in the automotive industry and set the foundation for future developments.
The 1970s saw significant advancements in industrial robotics technology. The introduction of microprocessors allowed robots to be equipped with sensors and vision systems, making them more intelligent and capable of handling complex tasks such as assembly and material handling. It was also during this time that Japan emerged as a dominant force in the robotics industry, with companies like Fanuc and Kawasaki Heavy Industries leading the way.
In the 1980s, computer-aided design (CAD) and computer-aided manufacturing (CAM) technologies were combined with industrial robotics, leading to the development of computer numerical control (CNC) machines. CNC machines are used to manufacture parts and components with high precision, accuracy, and speed, making them an essential tool in modern manufacturing facilities.
The 1990s saw a significant shift towards the use of robots in industries other than automotive, such as electronics, food processing, and pharmaceuticals. This decade also witnessed the development of collaborative robots or “cobots,” which work alongside humans in a shared workspace. Cobots have revolutionized the concept of human-robot collaboration, making it possible for smaller businesses to adopt industrial robotics.
In the 21st century, industrial robotics has continued to evolve at a rapid pace. With advancements in artificial intelligence and machine learning, robots are becoming more autonomous and can adapt to changes in their environment. They are also becoming more affordable and user-friendly, allowing small and medium-sized enterprises (SMEs) to incorporate them into their operations.
Types of Industrial Robots
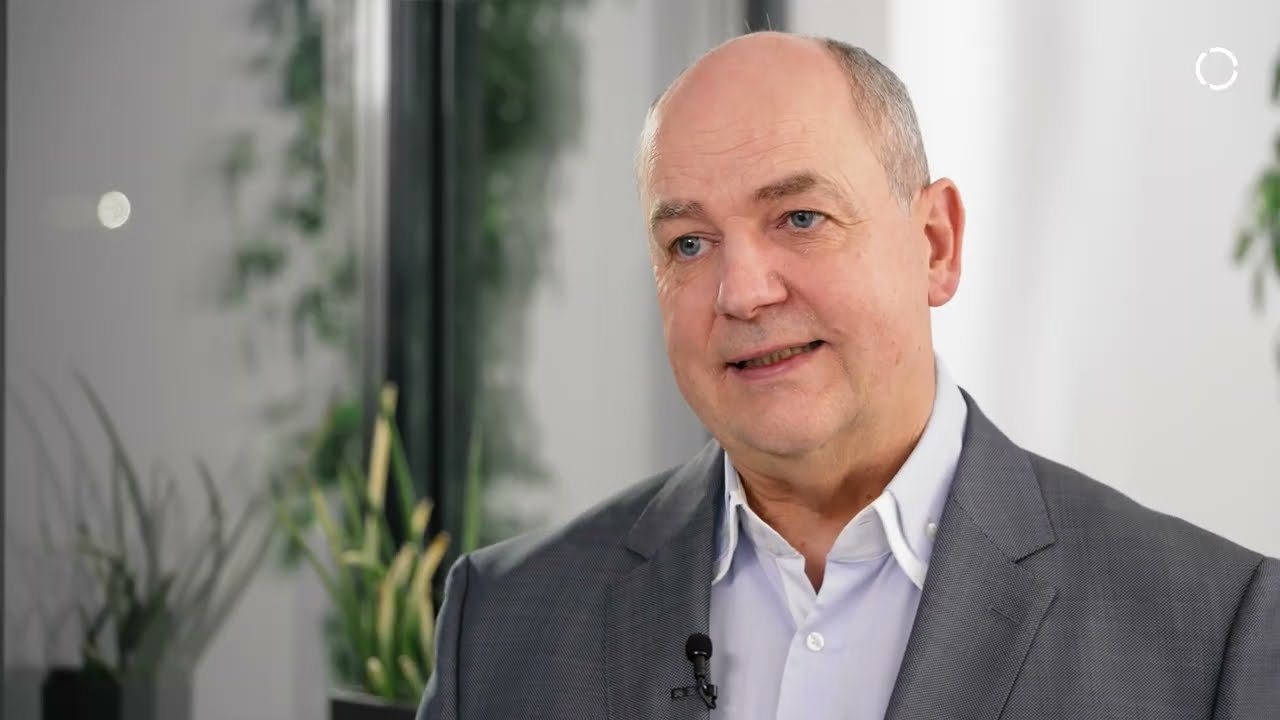
Industrial robots can be classified into various types based on their structure, movement, and application. The most common types of industrial robots include:
Cartesian Robots
Cartesian robots, also known as gantry robots or rectilinear robots, have three linear joints that move along three perpendicular axes. These robots are ideal for pick and place applications and are commonly used in material handling, packaging, and assembly processes.
SCARA Robots
Selective Compliance Articulated Robot Arm (SCARA) robots have two parallel-jointed arms that can move in the horizontal plane, with a vertical joint connecting them. This configuration allows for high-speed movements and precise positioning, making SCARA robots suitable for assembly and packaging tasks.
Articulated Robots
Articulated robots have multiple joints, similar to a human arm, allowing them to mimic human movements. These robots are highly versatile, with six degrees of freedom (DOF), and are used for tasks that require dexterity and flexibility, such as welding, painting, and assembly.
Delta Robots
Delta robots, also known as parallel robots, consist of three arms connected to a central base. These robots are designed for high-speed pick and place applications and are commonly used in the food and beverage industry.
Collaborative Robots
Collaborative robots, or cobots, are specifically designed to work alongside humans in a shared workspace. These robots are equipped with sensors and safety features that allow them to operate safely around humans. Cobots are ideal for small businesses or SMEs looking to automate their processes without major changes to their production line.
Applications of Industrial Robotics
Industrial robotics has found applications in a wide range of industries, including automotive, electronics, aerospace, pharmaceuticals, food and beverage, and consumer goods. Some of the most common applications of industrial robots include:
Welding
Welding is one of the earliest applications of industrial robotics. Robotic welders are used in the automotive, aerospace, and construction industries to perform tasks such as spot welding, arc welding, and laser welding. These robots offer high precision and consistency, resulting in better quality welds and reducing the risk of human error.
Material Handling
Material handling involves moving raw materials, components, or finished products within a production environment. Industrial robots are used for material handling tasks such as palletizing, de-palletizing, and loading and unloading. These robots are equipped with specialized end-effectors, such as grippers and suction cups, to handle different types of materials.
Painting
Robotic painting is commonly used in the automotive, aerospace, and consumer goods industries. Robotic painters offer superior precision and consistency compared to manual painting, resulting in better quality finishes. They can also be programmed to apply a uniform coating, reducing material waste and increasing efficiency.
Assembly
Industrial robots have revolutionized the assembly process, making it faster, more efficient, and less labor-intensive. Robots are used for tasks such as screwing, gluing, welding, and fitting components together. These robots are highly precise and can handle delicate or intricate parts that are difficult for humans to manipulate.
Inspection
With advancements in vision systems and sensors, industrial robots are now capable of performing various inspection tasks with high accuracy and speed. These robots use 3D scanners, cameras, and other sensors to detect defects, measure dimensions, and ensure product quality.
Advantages and Disadvantages of Industrial Robotics
Industrial robotics offers numerous benefits, but it also has its drawbacks. Some of the advantages and disadvantages of industrial robotics include:
Advantages
- Increased productivity: Industrial robots can work non-stop, without rest breaks, and at a faster pace than humans. This results in higher production rates and increased output.
- Improved product quality: Robots are incredibly precise and consistent, reducing the risk of human error and improving product quality.
- Cost savings: Despite the initial investment, industrial robotics can lead to long-term cost savings by reducing labor costs, minimizing material waste, and increasing efficiency.
- Reduced health and safety risks: With robots taking over dangerous and repetitive tasks, workers are exposed to fewer health and safety risks in the workplace.
- Flexibility and versatility: Industrial robots can be reprogrammed and reconfigured to perform different tasks, allowing manufacturers to adapt to changing production needs.
Disadvantages
- High initial costs: Implementing industrial robotics involves significant upfront costs, including the purchase of robots, training, and integration into existing systems.
- Limited adaptability: Robots are programmed to perform specific tasks and lack the adaptability and problem-solving skills of humans, limiting their use in certain applications.
- Job displacement: The increased use of industrial robots may lead to job losses in industries that rely heavily on manual labor.
- Complexity: Industrial robots require skilled technicians and programmers to operate and maintain them, making it challenging for small businesses or SMEs to adopt this technology.
Future Trends in Industrial Robotics
The future of industrial robotics looks promising, with advancements in technology and increasing demand for automation. Some of the key trends that are shaping the industry include:
Artificial Intelligence
The integration of artificial intelligence (AI) and machine learning (ML) into industrial robots is changing the game. These technologies enable robots to learn from data, make decisions, and adapt to changes in their environment, making them more autonomous and efficient.
Internet of Things
The Internet of Things (IoT) is enabling robots to communicate with each other and with other machines, resulting in a more connected and intelligent production environment. This allows for real-time monitoring and control of robots, leading to better performance and predictive maintenance.
Human-Robot Collaboration
Collaborative robots, or cobots, are expected to become more prevalent in the manufacturing industry, as they offer a safe and cost-effective solution for smaller businesses looking to automate their processes. Cobots will work alongside humans, taking over repetitive and dangerous tasks, while humans focus on more complex and creative tasks.
Mobile Robots
Mobile robots, such as self-driving vehicles and drones, are set to transform the logistics and transportation industry. These robots can move autonomously, reducing the need for human intervention, and streamlining the supply chain.
Conclusion
Industrial robotics has come a long way since its inception in the mid-20th century. With continuous advancements in technology and increasing demand for automation, industrial robots are set to become an integral part of modern manufacturing processes. While there are challenges and concerns surrounding the use of industrial robots, their benefits outweigh the drawbacks, and the future looks bright for this rapidly evolving industry. From welding and painting to assembly and inspection, industrial robotics has transformed the way we manufacture goods, leading to increased productivity, improved product quality, and a more efficient and safer working environment. The rise of the machines is not a threat, but rather a revolution that promises to drive economic growth, innovation, and a better quality of life for all.